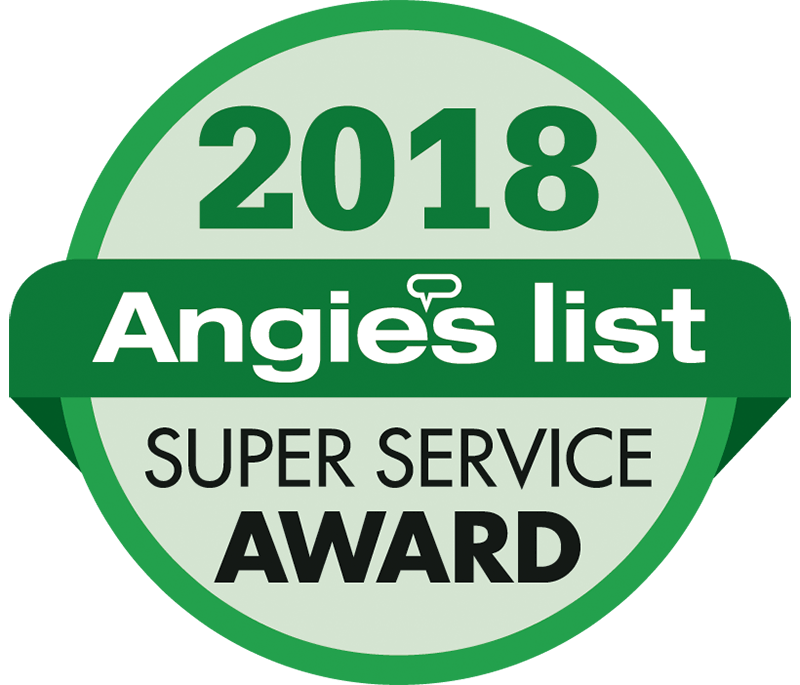
Our continued commitment to the craft was recognized again this week when AAA-1 Masonry & Tuckpointing was awarded the Angie’s List Super Service Award for 2018! This award honors service professionals who uphold the highest work standards and maintain exceptional service ratings and reviews. Fewer than 5% of all companies in the Angie’s List network receive this award. We are extremely grateful for the award and what it represents.
With winter beginning to loosen its grip on Chicagoland and January’s polar vortex now fading into memory, we are starting to make preparations for the 2019 work season. Let one our licensed project managers work with you to assess your masonry building and make recommendations for repair. We can be reached by phone (773/622-7300 in the city; 847/491-9700 in the suburbs) or e-mail (Info@AAA1Masonry.com). If you need to reacquaint yourself with the services we offer, please take a moment to peruse our easy-to-read website (www.AAA1Masonry.com).
Thank you for your continued support.
Rob
Post: Prohibition-Era Building Materials
Thursday January 31, 2019
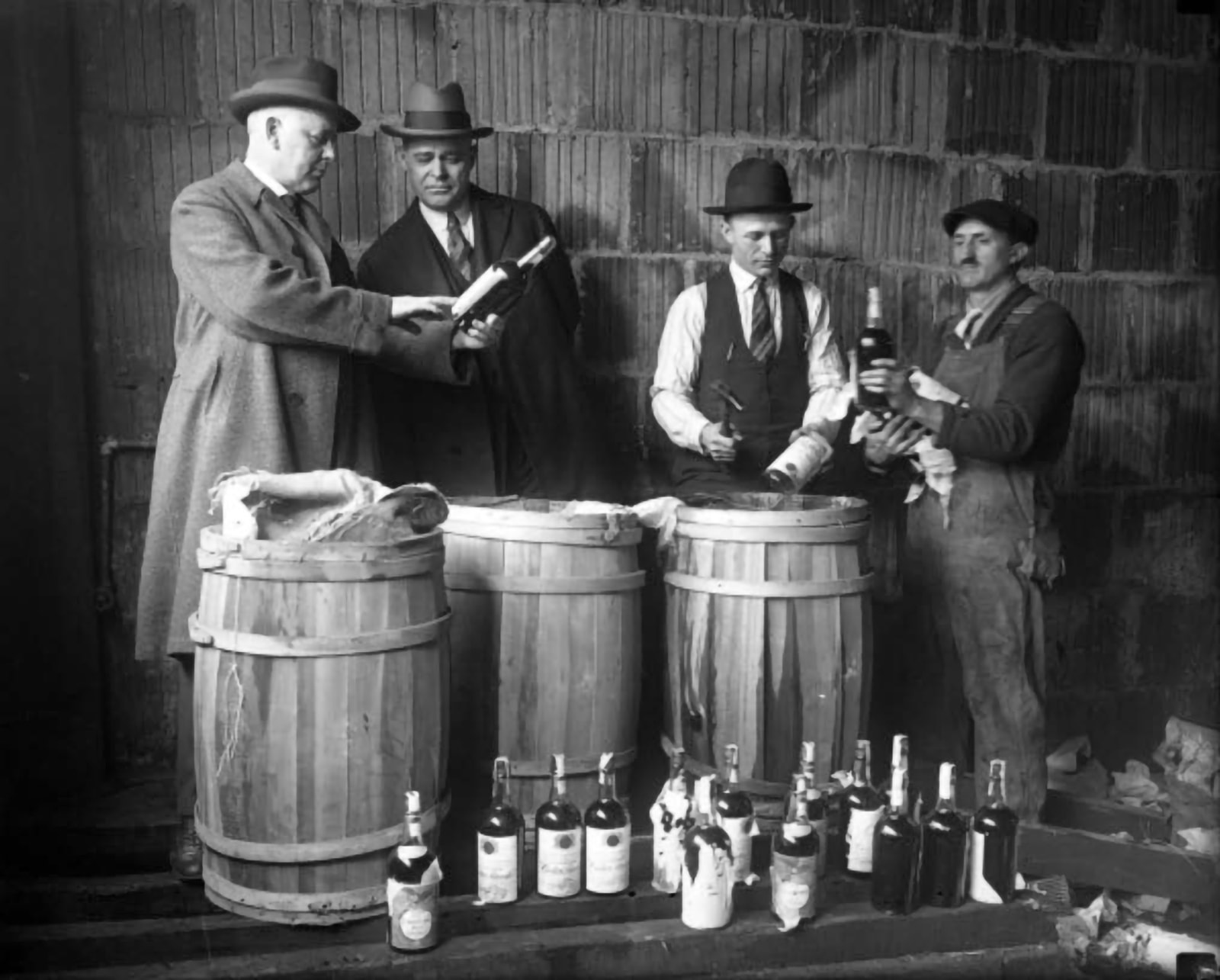
This image of a Prohibition-era liquor seizure crossed my desk recently and I thought the photograph was terrific in so many ways.
The image is obviously staged to show off the size of the seizure, praise the law enforcement officers who had a hand in making the bust, and communicate the fate of the contraband (see the officer third from left with hammer in hand).
The black and white image is well staged and side lit beautifully.
But what really caught my attention and put a smile on my face were the clay blocks used to construct the wall in the background! These 12” X 12” clay building blocks were commonly called “telephone blocks” because they were the size and thickness of a typical phone book.
These very durable building blocks were the forerunner to today’s much maligned cinder blocks, and we commonly find these telephone blocks in walls and ceilings under many coats of plaster and paint in older apartment buildings from Hyde Park to Lincoln Park to Wilmette. In many detached garages from the late 19th century through the 1940s, these phone blocks were used to divide up the space when it was horses (not automobiles) that were parked inside. Based on the presence of the water pipe and spigot in the lower left corner of the image (and, no doubt, the gas line leading to a radiator just beyond the right side of the photo), this garage was likely constructed in the very early 20th century.
The licensed masons at AAA-1 Masonry & Tuckpointing love to geek out over masonry from the bygone era.
If your former horse stable-cum-garage (or any other building for that matter) needs an honest assessment from an experienced masonry restorationist, we would love to help.
Thank you for your continued confidence in our work.
-Rob
Post: Recipient of the 2017 Angie’s List Super Service Award
Thursday February 1, 2018
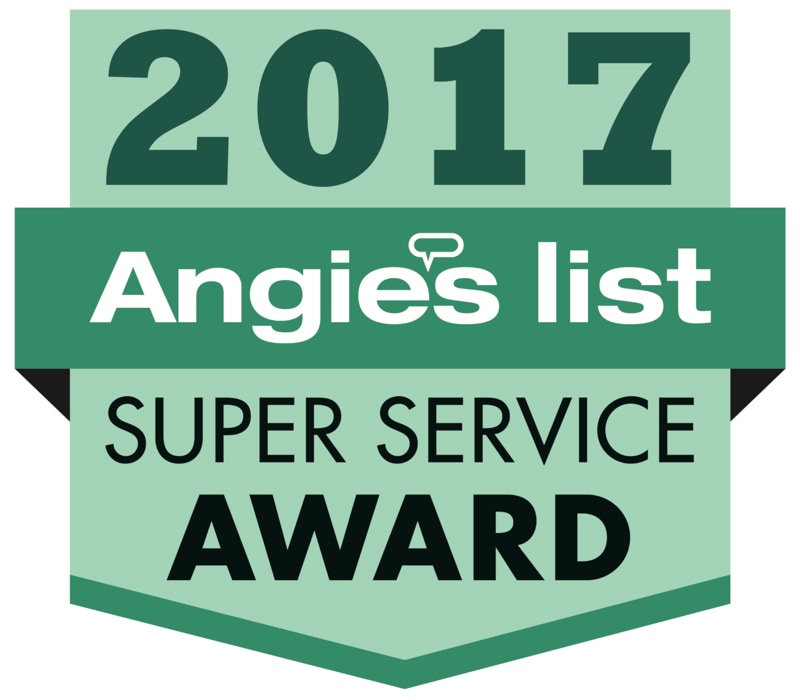
Even though many of us at AAA-1 Masonry & Tuckpointing have been restoring masonry structures well before the turn of the century (and certainly before organizations like Angie’s List even existed), it still feels good to be formally recognized for exceptional workmanship and service from such a well-recognized organization.
The Angie’s List Super Service Award is given to fewer than 5% of all contractors found on Angie’s List, and requires exceptional service ratings over the course of the year.
Sincere thanks to all of you for your kind praise and recognition of our commitment to the highest standards in the masonry arts.
Now in our 65th year of family ownership, AAA-1 Masonry & Tuckpointing specializes in mortar restoration (including historical mortar matching), brick replacement, chimney and parapet wall rebuilding, lintel replacement, caulking, cleaning and sealing. Call us for a free and informative consultation or request a proposal by clicking on the red button in the upper right corner of the screen.
Thank you,
Rob
Post: Repairing Mortar Joints in Lakeview
Sunday August 27, 2017
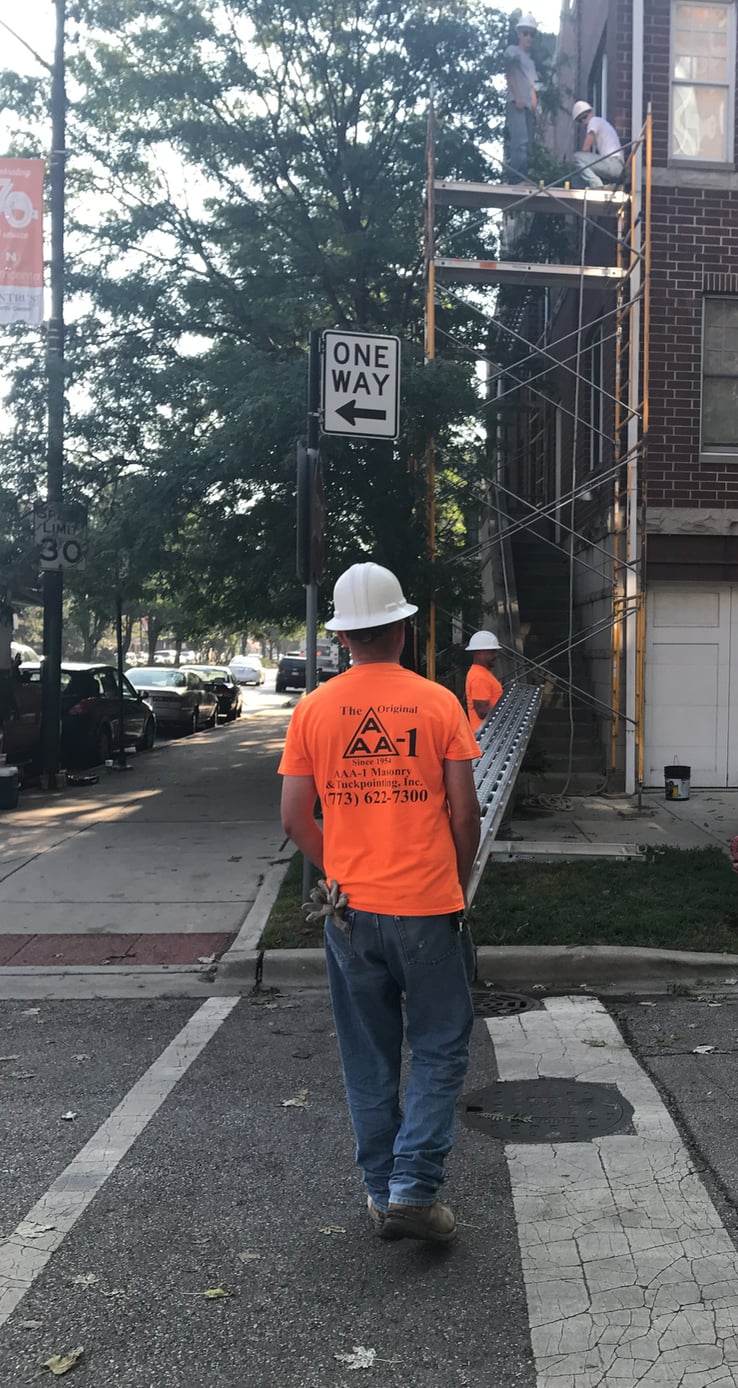
Just a quick post today! We're glad to be back at the Hermitage Court Condominium Association to address some standard masonry issues on this lovely masonry structure in the Lakeview neighborhood of Chicago. These owners are great, easy to work with, and really value the time and attention we spend making their building water tight. (Always nice working with clients who appreciate the quality of what you do!)
In this photo the men are setting up the necessary tubular pipe scaffolding and decking in order to access the third-story face brick mortar joints in need of repair. We'll be back to seal the wall with our 100% silane sealant after our new mortar has completely cured in a week’s time.
Thank you!
-Rob
Post: What's That Haze On My Bricks?
Tuesday August 15, 2017
Because of our commitment to quality restoration work, we get called out to address masonry issues on many very nice homes and buildings in Chicago, the North Shore and the Near West suburbs.
It's a real compliment and not one that we take lightly. So when we start to notice a whitish haze appearing more and more frequently on newer luxury homes and buildings we begin to get concerned (and curious).
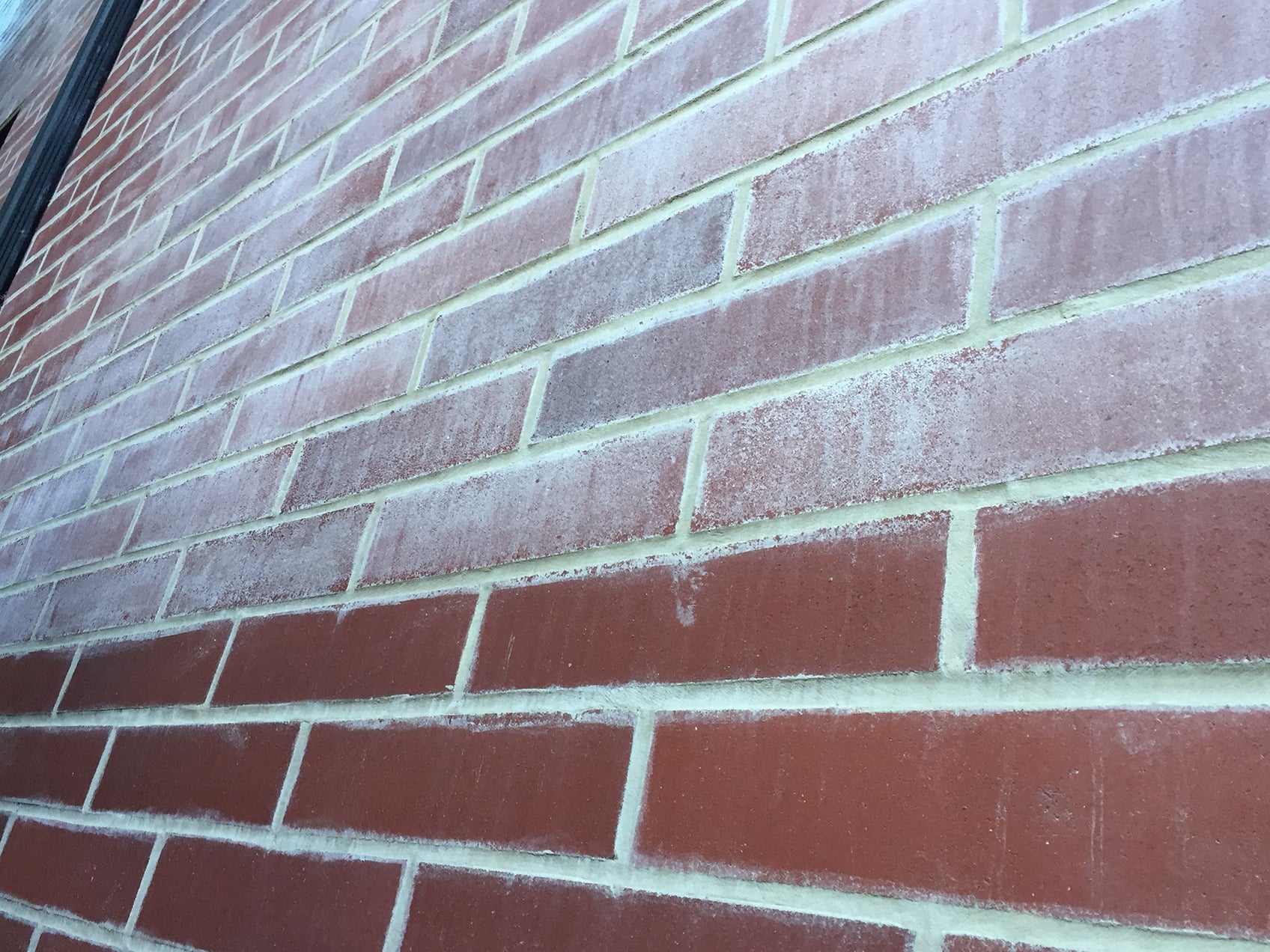
For those of you who know a thing or two about newer masonry structures, you might look at this photo and conclude this wall is suffering from extensive efflorescence, the condition whereby salts and other minerals leach out of porous masonry walls as they dry out. Brick efflorescence certainly would be a good guess.
But look at the lower several courses of the wall. These bricks have considerably less haze on them. (Actually the little bit of haze on the lower section of the wall looks like mortar sloppily brushed onto the face of the bricks by a previous contractor.) Typically, efflorescence does not stop so abruptly with such nicely demarcated boundaries as seen in this photo.
When I rubbed my fingers over the wall, it imparted a greasy film. When I sprayed water on the wall, the haze disappeared and the bricks returned to their bright red color...until the moisture evaporated and the bricks again appeared hazy.
As I later learned, the hazy section of the wall was sealed by another masonry company using an inexpensive water-based product that left the milky haze. Because the previous company did not seal the lower 6 feet of the wall, this was the only section that did not turn hazy. This water-based product appears to have been rolled on to the wall, which helps to explain the stark demarcation between treated and untreated wall. AAA-1 Masonry & Tuckpointing does not use water-based sealants because they do not penetrate as deeply into masonry substrates as our 100% silane solution.
Fortunately, we were able to use a masonry detergent and a hot-water power washer to remove about 75% of the hazy film from the wall.
Some very fancy-sounding masonry sealants do a poor job at repelling wind-driven rain and seem to leave a haze behind (e.g., Master Protect H177 Clear Sealer; and Enviro Double-Seven are two that come to mind).
Before you or your contractor brush, paint or spray any product on your masonry walls, test a small area of your wall with the product and make sure you like what you see. An ounce of prevention might save you a lot of disappointment and cost.
-Rob