Flashing or Through-Wall Flashing is a waterproof membrane used to stop moisture from penetrating porous masonry or to re-direct water out of a masonry wall. High quality flashings are composed of copper, lead-coated asphalt or other durable materials which do not degrade from long-term exposure to moisture or ultraviolet rays. When installed properly, flashings should extend the full width of the wall (or beyond) and are often paired with stainless steel drip edges.
AAA-1 Masonry & Tuckpointing was called out to a Lincoln Park residence to determine how water was infiltrating the dwelling. After removing the parapet wall capstones we discovered that the builder had used an inexpensive plastic membrane—the black material laid across the top of the wall—and had failed to size it correctly (refer to photo at left). Membranes must extend the full width of the wall in order to function properly, and here the flashings stopped a good two inches inside the walls rendering it completely ineffective. After disposing of the inappropriate flashing and allowing the wall cavity to dry out, we installed the correct flashing detail and re-set the capstones.
In this photo, AAA-1 Masonry & Tuckpointing is in the process of replacing a severely deflected third-story window lintel in a loft building in downtown Chicago. To the horizontal leg of the new window lintel we secured stainless steel drip edges in a continuous bed of caulk, and installed self-adhering Grace "Perm-A-Barrier" through-wall flashing and fastened it to the brick back-up wall using termination bars, masonry screws and caulk. On the right end of the masonry opening, we are in the process of installing a field-constructed end dam designed to prevent water from migrating into the masonry jamb. (Note how the glass window has been protected with Visqueen and painter's tape.)
Post: Extensive Edison Park Office Project (Underway)
Sunday April 24, 2011
AAA-1 Masonry & Tuckpointing performed a gut-rehab of an industrial office space in the Edison Park neighborhood of Chicago.
Extensive demolition work was performed over the winter including removal of the drop-ceiling tiles, the damaged carpets, the drywall and most of the plumbing. (In fact, just about everything but the door to the 60-year-old safe was in terrible condition and unable to be salvaged.)
After demolition work, it was decided that the exposed steel beams, wood roof rafters and Chicago common brick walls lent themselves to a terrific century-old industrial look. After creating larger openings for new windows and building new masonry walls for conference rooms and work space (and, yes, the original safe), everything was sandblasted to give it a rich glow.
Post: Wright Chimney Restoration
Tuesday March 15, 2011
AAA-1 Masonry & Tuckpointing was called out to this Frank Lloyd Wright home in Hyde Park to correct the significant deflection in this 80' tall chimney. Due to its historical significance the City of Chicago's Department of Preservation was consulted and provided guidelines for the work.
After scaffolding was erected and the building could be better evaluated, the chimney caps were determined to be one source of water infiltration and structural damage to the bricks below.
Years ago, an earlier repair of the chimneys consisted of a thin, sloppy and insufficient smear of mortar applied right over the original cracked and eroded mortar joints. Seasonal rains and snows continued to damage the chimney shaft to the point of the severe deflection.
Although the severity of the damage required that the chimney be dismantled, nearly all of the bricks themselves were found to be in very good condition. (This was fortuitous for the owners since bricks of this size, color and texture are no longer produced.) As the chimney was dismantled, the condition of every brick was evaluated. Structurally sound and visually pristine bricks were cleaned of excess debris to ensure proper mortar adhesion (new mortar will not bond well to bricks with bits of old mortar still clinging to them).
With the chimney brickwork almost complete, the final step was to hand-pour a custom-sized concrete chimney cap.
Post: Lincoln Park Residential Restoration
Thursday September 9, 2010
AAA-1 Masonry & Tuckpointing was called to restore the masonry gangway walls of a 100-year-old Lincoln Park single family home. As we often find on structures of this age the bricks here were severely spalled (i.e., delaminated), the mortar joints repaired numerous times with thin (and ineffective) smears of improperly applied mortar, and the fill under the sidewalk had settled unevenly so that the concrete gangway pitched toward the house. (See photo 1.)
And look at the condition of the bricks and mortar joints around that roof drain! (See photo #2.)
Was it any wonder the finished basement chronically flooded?
AAA-1 Masonry & Tuckpointing carefully dismantled the outer wythe of the brick walls and in doing so revealed numerous abandoned chimney flues and windows that the developer covered over. (See photo 3.)
To match the old coal soot-stained Chicago common bricks and mortar remaining on the upper floors of the home, we utilized a darker "clinker" brick and left the texture of the mortar in a rough unfinished condition. (See photos 4 and 5.)
Post: Critical Facade Inspection Work
Sunday August 15, 2010
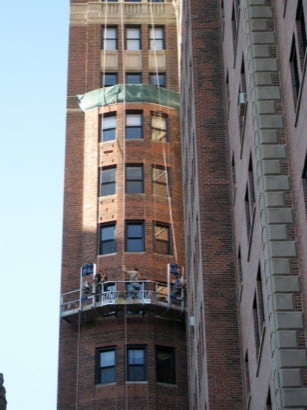
AAA-1 Masonry & Tuckpointing was called out to perform a critical facade inspection of a 16-story century-old building in the Lakeview neighborhood of Chicago.
Working in conjunction with an architectural/engineering firm, AAA-1 Masonry & Tuckpointing's licensed masons identified and corrected the defects in the facade while riding swingstage scaffolding custom built to accommodate the unique features of the building.
Annually, AAA-1 Masonry & Tuckpointing executes capital improvement projects and defect studies (for long-range budget planning) for dozens of condominium associations in the Chicagoland area and the suburbs. For an understanding of the inspection program required for your building, review the City of Chicago's Exterior Wall Maintenance Guidelines (PDF).