Despite the very cold weather this winter, the phones have been ringing steadily with landlords, property managers and homeowners desperate to stop the leaks coming through their exterior walls and into their living spaces.
Due to our region's Polar Vortex, it seems that many buildings' gutters and downspouts are frozen solid with ice. Even though the air temperature at high noon isn't even breaking zero, ice on the south sides of many buildings is melting a bit in direct sunlight and that runoff is causing leaks inside the units.
Because it is much too cold to make masonry repairs (when nighttime temperatures dip below freezing the mortar fails to cure properly), we have been installing a lot of heavy-duty vinyl tarps to masonry walls as a means of providing a physical barrier from the elements. The solution is 100% effective if the ice and snow in the affected area is first slowly melted with a blowtorch (perfectly safe for masonry walls) prior to tarp installation. What's neat about our tarps is their durability. If you don't mind having a tarp installed on the exterior of your building, our tarps may be left up indefinitely (i.e., many years) because they do not shred, rip or tear like the cheap tarps you may find in the big box stores. Once the tarp is installed, wind-driven snow and sleet are thwarted and water is no longer able to infiltrate the wall, allowing you to make the required repairs to the inside of your living space.
If you think your building would benefit from the installation of our heavy-duty vinyl tarps and secure fastening systems, please don't hesitate to give us a call 847/491-9700 (suburbs), 773/622-7300 (city), or e-mail us at Info@AAA1Masonry.com.
During this time of extreme weather, we ask that you look out for your neighbors and travel with caution.
Post: Why Weather Matters
Monday January 27, 2014
To date it has been a brutal winter in Chicago. This year, the arctic cold came almost a week before Thanksgiving and has not let up since. I remember the blizzard of 1979 quite clearly, but until this year I had never heard the term "Polar Vortex" nor heard a weatherman report windchills of 50 below zero.
As one of my foremen reminded me recently, 2013 was the shortest work season we've experienced due to inclement weather in the past 32 years (and he would know since he's been working with AAA-1 Masonry since then). Record-breaking spring rains and unending record-breaking cold starting in mid-November have made 2013 a season we are glad to put behind us.
Only a few days remaining in January and the historically cold winter shows no signs of letting up. And yet this week, as I drove the streets of Chicago, the North Shore and Oak Park clearing ice from customers' gutters and performing masonry inspections for 2014 spring work, I saw masons performing restoration work all over the place. In Oak Park, I saw brickwork being performed along the busy commercial stretch of Oak Park Avenue. In Chicago's Wicker Park, new construction projects along Damen Avenue were humming along.
I was aghast. Why? Because masonry work uses water—and lots of it—to make the mortar we use. (For the uninitiated, mortar is the very important glue which bonds together brick, stone, concrete block and terra cotta.) If the mortar freezes while it is curing—and it can take upwards of 4 weeks in cooler weather for mortar to cure completely—its strength, longevity and resistance to wind-driven rain can be compromised... sometimes significantly.
If you think you can cheat Mother Nature by adding accelerants or "season extenders" (which reduce the freezing point of the mortar mix for cold weather use), think again. These additives seriously compromise the quality and longevity of the mortar, and often lead to additional maintenance costs—costs which could be avoided completely if the mason were to respect the temperature restrictions of the mortar. If you hear a supposed mason telling you that it is okay to use mortar additives because everyone does it, you need to consider removing him from your project.
The actual point at which new mortar will freeze depends on a lot of factors, but a failsafe rule of thumb is this: If nighttime temperatures are going to dip more than a couple of degrees below freezing, then the weather is going to have a deleterious effect on your mortar (or on your concrete if you are pouring a foundation). And the colder it gets at night, the worse the impact.
I suppose that if you're a developer building a new residence and offer only a one-year warranty from date of completion on your work, you'll probably avoid a lawsuit from the new owners when, a few years down the road, the mortar begins to fail and the entire structure needs to be ground out, tuckpointed and sealed at a terrific cost. But if you're a mason with even a shred integrity, you know better and will not work with mortar when nighttime temperatures are going to drop more than a degree or two below freezing.
Here are two eager workers getting ready to pour concrete footers for a front porch in the Bowmanville neighborhood of Chicago. (You can see the red cement mixer in the center of the photo and the round yellow sonotube sticking out of the ground just behind the worker on the right.) The temperature was in the upper teens in the middle of the day when this photo was taken, and the evening forecast called for sub-zero temperatures (before accounting for windchill) and 2" - 4" inches of snow. Concrete and mortar require many days to cure properly, and if it freezes during this period it is as good as useless. Would you pay for this work?
The second-story concrete blocks used to build this masonry structure in East Lake View are frozen solid. (The dark patches are frozen water.) The home builders failed to wrap or heat the site. The daytime temperature was 12 degrees when this photo was taken; I wonder how much colder it got at night?!
But don't worry about the structurally compromised concrete block walls... you won't be able to see them after the builder throws the facade up over it!
Masonry work is being performed all over Chicago in these inappropriate weather conditions (it is unethical—but not illegal—to build in the dead of winter). The result is poorly constructed housing stock unable to withstand wind-driven rain and in need of increased and more costly maintenance.
Post: A Few Thoughts About Quality
Tuesday December 10, 2013
This week as I drove through Chicago, parts of the North Shore, Oak Park & River Forest, I was amazed at how much low-quality restoration work was being performed by folks passing themselves off as "masons." In most cities and suburbs in Cook and Lake Counties, individuals do not need to be licensed in the sense that they have been certified as "competent" or "expert" in the trade. Often, these people need only submit proof of insurance and pay a modest fee for a business license to be able to claim they are qualified to perform what is, in effect, surgery on your brick home or building. That's unsettling.
Recently I drove by a service vehicle which caught my eye (see below). A few things I have learned about this industry in my 20 years running the family business and this photo seemed to capture them.
1. A fancy truck does not a restorationist make. Lots of new trucks are purchased by folks looking to make a nice first impression. Many of these trucks are re-possessed a year later because the skill set of the mason driving the car falls far short of expectations.
2. If the tradesman cannot spell his trade properly (or does not catch the misspelling of his trade on the side of his fancy new truck), then he's probably going to miss some details on your project...or worse.
3. Tradesman should focus on one trade only. We've seen concrete driveway repairmen pass themselves off as masonry restorationists. We've seen roofers try to pass themselves off as masonry restorationists. Heck, we've even seen painters try to pass themselves off as masonry restorationists — what does a paintbrush have in common with a trowel? Tradesmen should focus on one trade and one trade only. For 60 years we've been focused solely on masonry restoration work (grinding & tuckpointing mortar joints, restoring bricks and lintels, washing, caulking and sealing masonry). Every one of the foremen at this company has been in the field performing masonry restoration work (and only masonry restoration work) for 28 years or longer. We do not roof, we do not pour concrete driveways, and we sure do not paint homes.
If you have a masonry issue, we would like to help.
Call us at the office or click here to leave an e-mail for Carolina, our terrific office manager, who will route your question or request for a proposal to one our veteran licensed project managers.
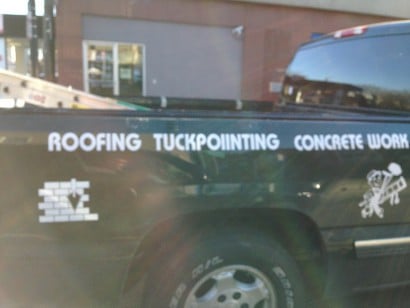
Post: If You Build It Right the First Time...
Saturday September 1, 2012
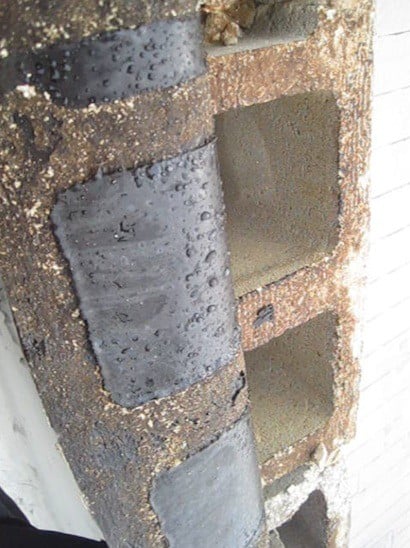
On almost a daily basis, AAA-1 Masonry & Tuckpointing receives calls from owners of newly constructed homes and buildings (i.e., structures built with concrete block or split-face block walls within the last 15 years) complaining of water leaks.
Because concrete blocks are mostly hollow and are so much more porous than bricks found in older structures, wind-driven rain usually blows right through the block walls and into the wall cavity. To limit the damage due to water infiltration through block walls, waterproof membranes are usually installed at each floor in a multi-story building and at the top of the parapet wall. Unfortunately, improperly installed flashings are very, very common in new construction dwellings and fail to stop water infiltration. That's why we see water marks on ceilings, and around balcony doors and windows in so many newer homes and apartments. Water infiltrations through concrete block walls short out electrical wiring, and burn out light switches and outlets, and are a real fire hazard. At a project in West Town (see photos), we pulled back a parapet wall's improperly installed flashing to discover water all over the underside of the material it was designed to repel. No wonder the block's hollow cells were soaked and the paint on the owners' bedroom walls were peeling!
Only when concrete block cells are grout-filled solid, and drip edges and membranes are sized properly and installed correctly can one be assured of a water-resistant flashing detail. All of AAA-1 Masonry's licensed masons know this. That's why after hundreds of parapet wall flashing installations we can boast a 99% success rate stopping water infiltration.
Post: More Common Than You Think
Friday July 6, 2012
These are birds-eye photos of a client's concrete block parapet walls after we removed the metal capping. Last we checked, empty cigarette packages, Coke bottles, and cardboard were not approved by the Department of Buildings as wall-reinforcing materials. They also do little to keep wall cavities dry. We grout-filled all of the accessible hollow concrete block cells, and installed through-wall flashing and stainless steel drip edges before installing properly sized quarried limestone capstones with cut drip edges.
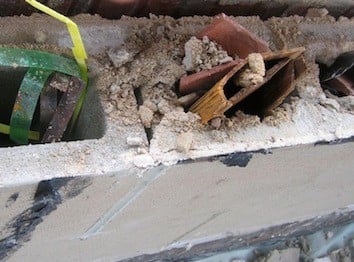
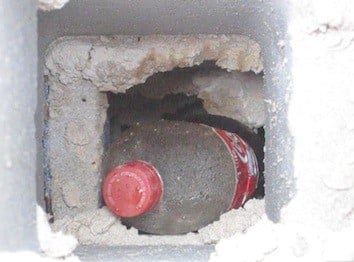
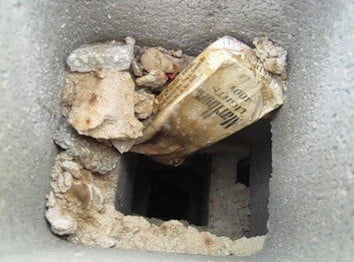